Raijintek Shows Off Pumpless Liquid Cooling System
by Anton Shilov on June 3, 2016 10:00 AM EST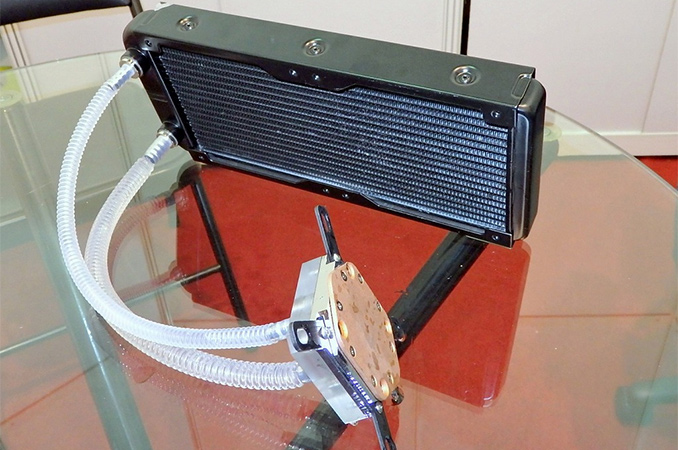
In the recent year’s all-in-one liquid cooling solutions gained significant popularity thanks to efficiency and quieter operation. However, even with those improvements, a closed loop cooler still needs a pump to enable circulation of liquid as well as at least one fan to maximize cooling efficiency. Seen as the next step, pumpless liquid cooling systems have been discussed by various developers for a while, and Raijintek demonstrated one at Computex 2016.
The prototype of Raijintek’s pumpless liquid cooling system is comprised of a completely passive CPU/GPU water block with a copper base (featuring a system of very thin channels to maximize heat dissipating surface area) with two nozzles of different diameter, two tubes as well as a radiator (images are by Hermitage Akihabara). The LCS is filled with a customized coolant, which has evaporation point of around 40°C to 50°C. Once the CPU or the GPU gets hot enough, the coolant turns into vapor and streams to the radiator through one of the tubes where it condenses back to liquid, whereas the cool coolant streams back to the water block.
Raijintek's prototype of a pumpless LCS. Image by Hermitage Akihabara.
Natural processes enable the circulation and the liquid cooling system is nearly noiseless (keep in mind that physical processes like water circulation create noises). In the best-case scenario, the higher is the temperature of the chip cooled down by such a LCS, the faster is the circulation. The theoretical limit of TDP that Raijintek’s prototype can handle is unclear, but different reports point to over 200 W, which is in line with traditional high-end and AIO liquid coolers. At Computex, the manufacturer demonstrated the prototype without any fans, but the radiator can be equipped with two of them to maximize cooling performance. While fans are not compulsory, there is a requirement, though: the radiator always has to be installed above the water block, which is something harder to do in small form-factor PCs.
Raijintek's prototype of a pumpless LCS. Image by Hermitage Akihabara.
The advantages of pumpless LCS are obvious: it does not have moving parts and therefore is more reliable than traditional systems; it does not generate as much noise and does not use power, provided that the coolant is cheap enough, the cost of a pumpless LCS should be lower than the cost of a traditional closed-loop liquid cooling system. On the other hand, it is completely unclear how the liquid with a very low evaporation point handles high TDPs when placed in a hot external environment. Besides, temperature of such liquid should remain below 40°C at all times (so, you are not going to use such device in Qatar, where temperatures above 40°C are common). Finally, the LCS must be perfectly sealed to maintain vacuum inside because any slight imbalance of pressure inside will harm its operation, a requirement that potentially increases the cost of the device.
Raijintek's prototype of a pumpless LCS. Image by Hermitage Akihabara.
Raijintek has invested a lot in development of its pumpless LCS over the years. In fact, the first prototype was ready back last year, but the company decided not to demonstrate it, but patent the technology in major markets first. Given the price of the new coolant as well as a new manufacturing process required to build pumpless LCS with vacuum inside, the price of the final product will not be low and may be actually higher compared to traditional AIO liquid coolers.
It is interesting to note that Raijintek is not the first to showcase a pumpless closed-loop liquid cooling system. Back in 2014, Silverstone demonstrated its prototype at Computex, but so far the company has not released it commercially.
Sources: BitTech, Hermitage Akihabara, TechPowerUp, 3DNews.
65 Comments
View All Comments
BurntMyBacon - Friday, June 3, 2016 - link
The issue is pressure. Most materials expand when they get hot (generally fluids more than solids). In a vacuum, it is easier for fluids to evaporate at lower temperatures. As the system heats up, more pressure is exerted by the fluids/gasses, but the copper heatpipes remain relatively rigid. This rise in pressure makes it more difficult to remain gaseous. Even when the whole system goes over the initial evaporation point of the system, the pressure build up ensures that the gas will condense back into a liquid, preserving the cycle. There are limits to how far different fluids can go, but that is the simple explanation. Cooper wax is just one potential medium that is often used in laptops due to not needing a vacuum to facilitate the melting / freezing cycle. Capillary action holds little meaning in this process. Cut open some heatpipes from CPU or GPU coolers and you'll likely find some liquid designs. Liquid / gas travels faster, removing the heat quicker, but needs a vacuum to work properly. You may find machined capillaries in some of these as well (I know Zalman has at least one design).In any of these rigid pipe designs, pressure and coolant expansion has a much greater effect on movement than gravity. Hence, CPU / GPU coolers don't have orientation requirements. So why does this one rely on gravity. It's because the tubes are not rigid. They are very flexible and prone to expansion, which prevents sufficient internal pressure buildup. This also explains the rather limited effective temperature range. Lack of internal pressure means that at a high enough (full) system temperature (think India), the system remains full gas and the natural movement cause by the evaporation / condensation cycle ceases to occur.
saratoga4 - Friday, June 3, 2016 - link
> Cooper wax is just one potential medium that is often used in laptops due to not needing a vacuum to facilitate the melting / freezing cycle.The metal you're thinking of is "copper". Cooper is a man who makes barrels. The inside of a heatpipe isn't vacuum, its filled with the saturated liquid and vapor-phase coolant. The "wax" doesn't have anything to do with pressure, it provides the capillary force to move the liquid coolant. Here is diagram explaining it:
http://image.slidesharecdn.com/heatpipe036-1306182...
The "wax" is typically a lot of fine copper wire, fiber, or sputtered on metal. Actual wax would result in no cooling because its not permeable. The capillary structure provides a lot of surface area which allows the capillary effect to wick coolant from the condenser back to the evaporator.
The fact that tubes are not rigid does not mean it must be gravity fed. They're not rigid because it doesn't really matter (the expansion of the pipes will be absolutely negligible relative to the expansion of the evaporating coolant) and this is clearly a prototype made from a watercooling system.
Spunjji - Saturday, June 4, 2016 - link
Thanks for the info, Saratoga4.BurntMyBacon - Monday, June 6, 2016 - link
@saratoga4: "The metal you're thinking of is "copper". ... The "wax" doesn't have anything to do with pressure, it provides the capillary force to move the liquid coolant."Actually, I just assumed that I don't know every thing there is to know about heat pipes. I've seen this stuff in laptop heat pipes before, but never know what it was called. I (apparently incorrectly) assumed that since the poster called it Cooper wax, that it was called that. Thanks for correcting me on this. In any case, I agree that no pressure control is necessary when this structure is in play.
BurntMyBacon - Monday, June 6, 2016 - link
There is more than one way to make a heat pipe, but apparently it is spam to link the relevant articles here (you can start at wikipedia). Most of my experience with heat pipes was not on PCs. While I'm fairly sure some of these used vacuum in the past (I feel old now), apparently the use of incompressible gasses is more common now. Increasing pressure rather than decreasing it would allow for the use of different carrier substances. The use of an outer wick was still common in the heat pipes I worked with to more efficiently return condensed fluid back to the heat block. It is probable, given that the build process is much cheaper when you don't have to trap gas (inside or out), that these are no longer widely used for PCs (does that make me outdated (0_0) ). I had thought that laptop style heat pipes were extremely sensitive to differences in condenser / evaporator elevations. Perhaps you know more about how they got around this issue. You can look up Variable Conductance Heat Pipes (VCHPs) and Pressure Controlled Heat Pipes (PCHPs).@saratoga4: "The fact that tubes are not rigid does not mean it must be gravity fed."
If it had some structure to provide capillary action to return condensed fluid back to the heat block, I agree. However, I don't see such a structure in play here (perhaps I'm missing it). I would guess that they are using a thermosyphon here.
samer1970 - Friday, June 3, 2016 - link
heatpipes are not flixable and add weight on the motherboard ...this one the weight is on the case ... not the motherboard .
invinciblegod - Friday, June 3, 2016 - link
Does the performance improve if you install it with the radiator is installed higher than the heatsink so the liquid falls with gravity and the hot vapor rises?DanNeely - Friday, June 3, 2016 - link
According to the article this is an actual requirement of the design.Shadowmaster625 - Friday, June 3, 2016 - link
Wouldnt the steam just bubble up both tubes simultaneously? How would you get flow? Why even have two tubes?londedoganet - Friday, June 3, 2016 - link
I assume that there are valves at the ends of the hoses to allow for circulation in one direction and not the other, and that the two hoses are to allow for the coolant to make a complete circuit of the heat exchanger?